Quality Assurance Efforts
- Improving the Quality of the Development & Productive Process
- Responding to the Quality Standards of Each Country
- Maintaining and Improving Quality and Customer Satisfaction
Improving the Quality of the Development & Productive Process
While considering it important to achieve greater quality in the upstream business processes for manufacturing, we aim to raise the quality not only of products and services that we introduce to the market but also the development and productive process itself.
For new products that we develop, our Quality Assurance Department checks the design reviews that are performed at every stage, from product planning stage to production planning stage. This is to ensure that quality is designed into our products and production processes.
At our Tire Technical Center, we are verifying RPA (Robotic Process Automation), a software technology that automatically processes routine tasks, to see how much it improves our operational efficiency by preventing risks that might manifest themselves in the course of business, such as human errors and fraud. Preparations are well underway for its full-scale introduction. By the end of fiscal 2019, its scope of application was expanded to cover general affairs and design work. In fiscal 2020, RPA was introduced to four routine tasks, successfully slashing the time taken to do the tasks by 929 human-hours, marking a total reduction of 1,194.5 human-hours since its inception.
Responding to the Quality Standards of Each Country
Against the background of, for example, climate change and expanding demand for mobility resulting from population increase in emerging countries and economic expansion, more and more countries and regions are rapidly introducing new laws and systems relating to performance and environmental quality for improving fuel efficiency of automobiles and reducing of CO2 emissions from automobiles. We are working to strengthen our handling of quality standards throughout the Group by responding to all quality related to increasingly complex laws and regulations.
At the four tire experiment/evaluation bases in Japan, we test our tires in compliance with ISO/IEC17025 (general requirements for the competence of testing and calibration laboratories). Since the initial accreditation in 2013, we have been making constant efforts to improve the accuracy and reliability of our testing.
Every year, our Tire Business and Automotive Parts Business each hold a Global Quality Management Committee (QMC) meeting, where quality assurance managers and others concerned come together from manufacturing bases from around the world. At this meeting, we share and discuss initiatives related to product quality, improvement of the quality system for production, the logistic and supplier quality demanded by customers (business partners).
ISO/IEC 17025 certificate
Examples of efforts to respond to quality standards
- Collecting information locally
- Making recommendations by participating in industry organizations
- Exchanging opinions with regulatory institutions
- Distribute information on the latest legal and regulatory trends
- Giving presentations related on legal and regulatory matters
Proprietary Technology to Meet the World’s Most Stringent Requirements in Europe
Relationship between Rolling Resistance and Wet Grip Performance
More and more countries and regions are introducing new laws and systems requiring better fuel efficiency and reduction of CO2 emissions from automobiles in the midst of changing climate, population increase in developing countries, and a need for more mobility resulting from economic expansion.
The role of tires is also becoming more important in improving fuel efficiency. Reducing the friction (rolling resistance) between tires and road surface will allow tires to roll easier so that vehicles can run further with same amount of fuel. Less friction means better fuel efficiency, but this generally means a weaker grip, lowering the tires’ ability to stop. This makes a big difference especially on wet roads. When designing fuel efficient tires, we must maintain good wet grip while reducing rolling resistance.
In Japan, the industry established a self-regulated “labeling system” in 2010 with ratings for rolling resistance and wet grip performance. Only tires that meet certain ratings in both categories can be labeled “fuel efficient”.
In Europe, there is a strict regulation requiring all tires for passenger vehicles sold within the EU to be labeled with ratings for rolling resistance, wet grip, and noise levels since 2012. In 2018, companies could not manufacture any tires for the EU if they do not meet certain level of performance in these categories.
We continue to improve our overall technical capabilities by designing high-performance tires for the European market with most stringent requirements. We can improve the standards in other countries and regions by making these high-performance tires available to the rest of the world.
The Labeling System in Japan (left) and in the EU (right).
Maintaining and Improving Quality and Customer Satisfaction
We understand that we are linked to customers and society through our products and services, and we will strive every day to maintain and improve product quality at our production sites. We are also conscious of efforts to improve our “quality as a company” at all workplaces and we are working to provide the “customer first” products and services.
We continually conduct product satisfaction surveys in markets where they are currently available and feedback customer requests to the design and production sites.
For more than 50 years, the Toyo tire group has undertaken QC circle activities to take the initiative to raise the level of quality management using what we have learned from a frontline perspective.
With their origins on the shop floor, Quality Control (QC) circles have now spread to sales departments, and today, about 300 circles are in operation within the Group. At all the circles, members bring with them their experiences and knowledge in order to resolve issues as well as working to improve quality by ascertaining current conditions, setting goals, developing activity plans, and analyzing issues.
Activities for improving service quality at sales companies
We want our customers to shop for our products with ease, confidence, and satisfaction. So, we are working hard to improve the level of service provided by sales associates and receptionists at our tire sales subsidiaries.
For example, Toyo Tire Japan Co., Ltd. (Japan) and independent distributors in Japan conduct work-specific training to train human resources so that they possess the required level of service quality for their respective work types (sales, reception, engineering). We also hold the National Speech Contest for our sales associates and “National Front Desk Call Handling Contest” for the receptionists. They are designed to encourage employees to be cognizant of their communication skills and learn how to explain the benefits of our products properly and in a way that is easy to understand.
The National Speech Contest is an opportunity for each business unit to showcase their solutions made possible by our products, such as solutions that our truck and bus tire unit offers to address challenges in the transport businesses, including rising costs and stricter fuel efficiency standards. By participating in this event, our employees develop an understanding that their services contribute to the solution of issues not only for individual customers but also for society as a whole, the realization of which manifests and increases motivation.
To prevent the further spread of COVID-19, we decided to cancel the contests in fiscal 2020, but we will resume activities in this regard once social conditions permit.
Tire Safety Awareness Activities
Every time our customers contact us with an inquiry or a complaint, we consider this as an opportunity to gain an understanding of the expectations of the Group and to improve our products and services.
FY2020 Tire Safety Awareness Campaign
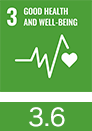
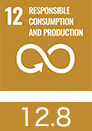
As a manufacturer/distributor of tires, on which the safety of the mobility society hinges, the Toyo Tire Group considers it a mission of great importance to educate drivers about the proper use of tires.
As more people choose to drive during the pandemic, it is nothing short of necessary to draw drivers' attention to safety by reminding them of the importance of periodic checks of tire pressure and precautions to observe when driving on a rainy day. Therefore, TOYO TIRE and its sales subsidiary in Japan, Toyo Tire Japan Co., Ltd., joined hands together like last year to engage in a tire safety awareness campaign.
In fiscal 2020, the campaign took place at four large shopping malls across the country with thorough measures in place to prevent infection with COVID-19. Using a driving simulator featuring our original software, we provided a total of nearly 500 drivers with a realistic experience of a variety of situations: driving on tires with different tread depths or levels of air pressure to compare breaking distance in rainy weather and handling stability, respectively, and driving a car that is hydroplaning. In a questionnaire survey after the experience, as many as 96% of the respondents said that they are now more conscious of the safety of tires.
We will continue organizing these educational campaigns in the hopes that drivers will take a greater interest in tires and start using them properly.
Responding to feedback from consumers
The Toyo Tire Group carefully listens to every piece of feedback that our customers (consumers) send on a daily basis, as we believe that they provide us with opportunities to understand their expectations for the Group and improve our products and services.
In fiscal 2020, our Customer Relations Department received a total of 2,207 consultations in Japan. The department responds to consultations received over the phone or on our website both accurately and simply.
We also analyze the nature of consultations and inquiries that we receive and send the findings to departments concerned to make our products and services easier to use. Such efforts have led to the development of the OPEN COUNTRY series, our flagship SUV tires enjoying immense popularity in the market, and improved visibility of our catalogues and websites.
We take customer feedback seriously as we believe that attempting to solve their problems and dissatisfactions promptly and satisfactorily with cooperation from our sales offices and technical service teams will help us to build a good and long-lasting relationship with customers.
Sustainability
- Message from the President
- TOYO TIRE Value creation
- TOYO TIRE Sustainability
-
TOYO TIRE Materiality
- Help create a society of sustainable mobility / Support the enjoyment of mobility for all
- Support diverse talent with motivating challenges and job satisfaction
- Continue innovating next-generation mobility technology
- Pursue decarbonization in all corporate activities
- Promote supply chain sustainability
- Ensure the fundamentals of manufacturing: quality and safety
-
ESG Activities
- E: Environment
- S: Upholding human rights
- S: Managing occupational health and safety to global standards
- S: Crisis management (responding resiliently to natural disasters, infections and other crises)
- S: Working with local communities (Helping solve local issues)
- G: Sound governance
- G: Compliance
- G: Risk management
- G: Information security
- G: Promoting digital transformation (borderless and centralized business management through ERP reform)
- External Recognition
- Report Library
- ESG Data
- ESG Data/Survey Index
- GRI Content Index
- Communication on Progress (CoP) Index
- Editorial Policy