Training Human Resources with Technical Expertise
Training Human Resources with Technical Expertise
With an eye toward a future in which the market environment is projected to be dramatically different due to the mobility revolution, TOYO TIRE is focusing its efforts on training professionals who can transform difficulties and crises into opportunities for sustainable growth. Human resource training supports technological innovation, the backbone of our Group, and we will engage in education and training that focuses on basic knowledge education, exchanges with parties outside the company, and passing on technology.
For example, Toyo Tire Corporation aims to train human resources with “problem-solving skills and innovative capabilities” based on thinking oriented toward customer needs as well as “logical thinking and facilitation capabilities,” which are important abilities. This will be done through company-wide, grade-specific training. At each of our technical headquarters, we will conduct training for young employees so that they acquire technical expertise and promote annual human resource training to achieve each organization’s mission.
In 2020, we included an SDGs course in the training curriculum for engineers. Through group work, trainees are expected to recognize technological development's role in resolving various social issues relevant to our business. On the production side, we are focusing on the enhancement of quality control personnel's inspection skills and the development of operators' multi-tasking skills.
Main training programs implemented in Japan (FY2020)
- Basic courses for young employees by mid-level employees
- Competency development courses for mid-level employees by outside lecturers
- Participation in outside training courses
Holding of the 10th Company-wide Technology
Development Presentation
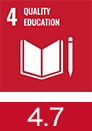
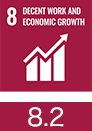
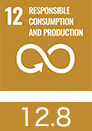
At Toyo Tire Corporation, technological development that meets customer needs and responds to the opinions of the Production and Sales Departments is conducted while constantly keeping commercialization in mind. In addition, we hold a company-wide technology development presentation as a venue to present the Company’s cutting-edge technology-related efforts and their results to management.
In FY2020, three out of the seven entries were commended after being evaluated based on the five criteria of originality, logic, future prospect, speed of development, and presentation.
Award Recipients of the 10th Company-wide Technology Development Presentation
- Outstanding Technological Development Award
Development of a vehicle performance evaluation model by way of 1D CAE:
The recipient developed simulation technology that predicts vehicle vibrations by creating a vehicle model that links tires and auto parts. - Unique Award
Efficient use of materials informatics (MI) in materials development:
The recipient developed fundamental technology that efficiently predicts materials' performance and structures through the combination of data accumulated on various materials and AI technology - Surprise Award
Development of an eco-friendly cure adhesion system:
Tires' characteristics and safety are attained by combining various materials. The recipient developed a cure adhesion system (using metallic fibers as a key component to ensure durability) that is safer and more friendly to the environment and organisms.
Sustainability
- Message from the President
- TOYO TIRE Value creation
- TOYO TIRE Sustainability
-
TOYO TIRE Materiality
- Help create a society of sustainable mobility / Support the enjoyment of mobility for all
- Support diverse talent with motivating challenges and job satisfaction
- Continue innovating next-generation mobility technology
- Pursue decarbonization in all corporate activities
- Promote supply chain sustainability
- Ensure the fundamentals of manufacturing: quality and safety
-
ESG Activities
- E: Environment
- S: Upholding human rights
- S: Managing occupational health and safety to global standards
- S: Crisis management (responding resiliently to natural disasters, infections and other crises)
- S: Working with local communities (Helping solve local issues)
- G: Sound governance
- G: Compliance
- G: Risk management
- G: Information security
- G: Promoting digital transformation (borderless and centralized business management through ERP reform)
- External Recognition
- Report Library
- ESG Data
- ESG Data/Survey Index
- GRI Content Index
- Communication on Progress (CoP) Index
- Editorial Policy